Downhole tool repair is a critical part of the oil and gas industry. The tools used deep within the earth’s surface must withstand extreme conditions, including high pressure, heat, and harsh chemicals. These tools are essential for drilling and production processes, so keeping them in good condition is a top priority. Over time, downhole tools experience wear and tear, which can lead to damage or malfunction. To address these challenges, the industry has developed many innovations in downhole tool repair to improve efficiency, reduce downtime, and increase the lifespan of tools. In this article, we will explore the latest innovations in downhole tool repair and how they are making a difference in the industry.
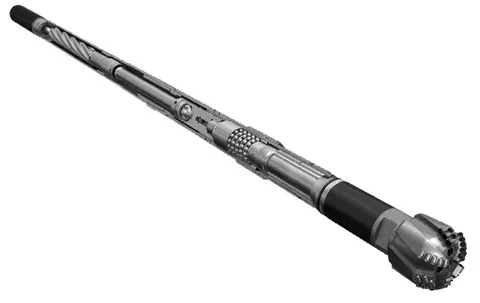
Why Are Innovations in Downhole Tool Repair Important?
Before diving into the innovations, it’s important to understand why advancements in downhole tool repair matter.
Reducing Downtime
When downhole tools fail or need repairs, drilling operations must stop. This downtime can be very costly for companies. Innovations in downhole tool repair aim to minimize the time it takes to fix or replace these tools, allowing operations to resume quickly and reducing financial losses.
Extending Tool Life
Downhole tools are expensive, and constantly replacing them is not cost-effective. New repair techniques focus on extending the life of these tools by addressing damage more effectively and preventing future issues.
Improving Safety
Innovations in downhole tool repair also contribute to safety. Damaged tools can cause accidents or lead to dangerous situations. By improving repair methods and ensuring tools are in good working condition, companies can create a safer work environment for their employees.
Reducing Environmental Impact
Better repair processes can also reduce the environmental impact of drilling operations. By reusing and repairing tools instead of discarding them, the industry can cut down on waste and reduce the need for new materials.
Latest Innovations in Downhole Tool Repair
The oil and gas industry has embraced several new technologies and methods to improve downhole tool repair. Let’s take a closer look at some of these innovations.
1. Advanced Diagnostic Tools for Early Detection
One of the most significant innovations in downhole tool repair is the development of advanced diagnostic tools. These tools help technicians identify problems before they become serious, allowing for early repairs.
Remote Monitoring Systems
Remote monitoring systems allow companies to track the condition of downhole tools in real-time. These systems use sensors placed on the tools to collect data on temperature, pressure, and vibration. The data is sent to technicians, who can analyze it and detect any signs of wear or malfunction. By catching problems early, technicians can schedule repairs before a major failure occurs, preventing costly downtime.
Non-Destructive Testing (NDT)
Non-destructive testing is another advanced diagnostic technique that allows technicians to inspect tools without damaging them. NDT methods, such as ultrasonic testing and X-ray inspection, can reveal cracks, corrosion, or other hidden issues inside the tool. This helps technicians make more accurate repairs and ensures that tools are safe to use.
2. 3D Printing for Custom Repairs
3D printing, also known as additive manufacturing, is a revolutionary technology that is now being used in downhole tool repair. This innovation allows technicians to create custom parts for tools quickly and efficiently.
On-Site 3D Printing
One of the main advantages of 3D printing is that it can be done on-site. If a downhole tool needs a replacement part, technicians can use a 3D printer to create the part right at the drilling site. This eliminates the need to wait for parts to be shipped from a manufacturer, significantly reducing downtime.
Customizable Designs
3D printing also allows for the creation of customized parts. If a tool needs a specific shape or size of component, technicians can design and print the part to fit perfectly. This level of customization makes repairs more efficient and ensures that tools are restored to optimal performance.
3. Laser Cladding for Surface Repairs
Laser cladding is another innovative technique used in downhole tool repair. It involves using a high-powered laser to melt metal powder and apply it to the surface of a tool. This process creates a new layer of material that bonds with the original tool, repairing any damage and providing extra protection.
Strengthening Worn Surfaces
Laser cladding is especially useful for repairing worn surfaces on downhole tools. Tools that experience constant friction, such as drill bits or pipes, often develop surface wear. Laser cladding can restore these surfaces, making them as good as new and extending the life of the tool.
Corrosion Resistance
In addition to repairing wear, laser cladding can also improve a tool’s resistance to corrosion. The new layer of material applied during the cladding process can be made from metals that are more resistant to rust and chemical damage, which is important in the harsh downhole environment.
4. Robotics for Precision Repairs
Robotics is playing an increasingly important role in downhole tool repair. Robots can perform repairs with greater precision than humans, and they can operate in environments that may be too dangerous or difficult for people to access.
Remote-Controlled Robots
Remote-controlled robots are used to perform repairs deep within wells. These robots are equipped with cameras and tools that allow technicians to inspect and repair downhole tools without having to remove them from the well. This speeds up the repair process and reduces the need for heavy equipment to pull tools out of the ground.
Automated Repair Systems
Some companies are also developing automated repair systems that use robots to carry out repairs on their own. These systems can identify problems, make repairs, and test the tool without human intervention. This not only saves time but also ensures that repairs are done with a high level of accuracy.
5. Advanced Coatings for Improved Tool Protection
Another innovation in downhole tool repair is the use of advanced coatings to protect tools from damage. These coatings are applied to the surface of tools to shield them from wear, corrosion, and other environmental factors.
Ceramic Coatings
Ceramic coatings are highly resistant to heat and wear, making them ideal for downhole tools that are exposed to extreme temperatures. These coatings can be applied to tools such as drill bits, stabilizers, and other equipment that faces constant friction and heat. By applying ceramic coatings, technicians can extend the life of these tools and reduce the need for frequent repairs.
Anti-Corrosion Coatings
Downhole tools are often exposed to corrosive chemicals and water, which can cause rust and damage over time. Anti-corrosion coatings, such as those made from specialized metals or polymers, provide a protective barrier that prevents rust and chemical damage. These coatings are particularly useful for tools used in offshore drilling, where exposure to saltwater is a major concern.
6. Predictive Maintenance for Proactive Repairs
Predictive maintenance is a cutting-edge approach to downhole tool repair that uses data and analytics to predict when a tool is likely to fail. By analyzing data from remote monitoring systems and other diagnostic tools, companies can forecast when a tool will need repair and schedule maintenance before a failure occurs.
Machine Learning and AI
Machine learning and artificial intelligence (AI) are key technologies behind predictive maintenance. These systems analyze data from downhole tools, looking for patterns that indicate wear or damage. Over time, the AI system learns to predict when a tool will need repair, allowing technicians to take action before a failure happens.
Reducing Unexpected Failures
Predictive maintenance helps reduce the risk of unexpected tool failures, which can lead to costly downtime and safety hazards. By knowing when a tool is likely to fail, companies can plan repairs in advance, ensuring that the tool is fixed before it causes any problems.
7. Digital Twins for Tool Simulation and Testing
A digital twin is a virtual model of a physical object, such as a downhole tool. This technology is being used in the oil and gas industry to simulate and test downhole tools in a virtual environment before they are used in the field.
Simulating Tool Performance
By creating a digital twin of a downhole tool, technicians can simulate how the tool will perform under different conditions. This allows them to identify any potential issues before the tool is deployed, reducing the likelihood of failures.
Testing Repair Solutions
Digital twins are also useful for testing repair solutions. Before making repairs, technicians can simulate different repair methods on the digital twin to see which one will be most effective. This ensures that the repair process is optimized and reduces the risk of further damage to the tool.
Conclusion: The Future of Downhole Tool Repair
The latest innovations in downhole tool repair are transforming the oil and gas industry. From advanced diagnostic tools that detect problems early to 3D printing and robotics that speed up repairs, these technologies are making it easier to keep downhole tools in good working condition. As the industry continues to evolve, we can expect even more breakthroughs in downhole tool repair that will further improve efficiency, safety, and sustainability.
For companies involved in oil and gas drilling, staying up to date with these innovations is essential. By adopting the latest repair techniques and technologies, companies can reduce downtime, extend the life of their tools, and ensure that their operations run smoothly and safely.
For more insightful articles related to this topic, feel free to visit penwhatmatters.com